Task
The availability of turbomachinery such as centrifugal pumps is often limited by their dynamic behavior. As a result of dynamic excitation by operating forces or imbalances, a response of the overall system occurs which is decisively influenced by the induced forces in narrow annular gaps, as they exist in journal bearings. In media-lubricated journal bearings of centrifugal pumps, these induced forces are significantly influenced not only by the hydrodynamic effect but also by axial flow. In addition, turbulent flow conditions can occur as a result of larger bearing clearances and significantly lower viscosities of the lubricants present. This laminar or turbulent flow present in the gap defines both the rigidity of the bearing arrangement and the decay behavior of any vibration that occurs. If the design is based on insufficient knowledge of the respective effects, resonance can occur in the worst case and subsequently lead to total failure of the machine and to maintenance-related and costly downtimes of the entire industrial plant.
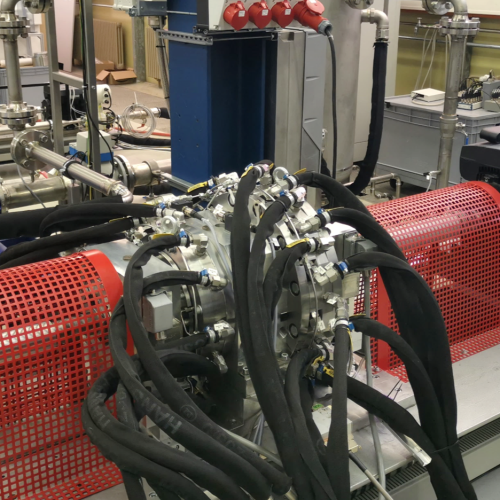
Experimental validation
In the course of the project, two unique journal bearing test rigs for the experimental identification of media-lubricated journal bearings were expanded at the Chair of Fluid Systems at the Technische Universität Darmstadt. The test rigs allow the experimental investigation of laminar as well as turbulent flow within the lubrication gap. In addition, they offer the possibility to determine the coefficients for the rotational degrees of freedom of the shaft in addition to the classical rotordynamic coefficients for purely translational motions.
Aim
The aim of the project was the development of a comprehensive database of rotordynamic coefficients and the identification of unstable operating conditions as well as the experimental validation of improved numerical calculation models for dynamic operating conditions based on an extended Reynolds differential equation, as well as the Clearance-Averaged Pressure Model for media-lubricated journal bearings in pumps developed on the basis of the integro-differential approach.
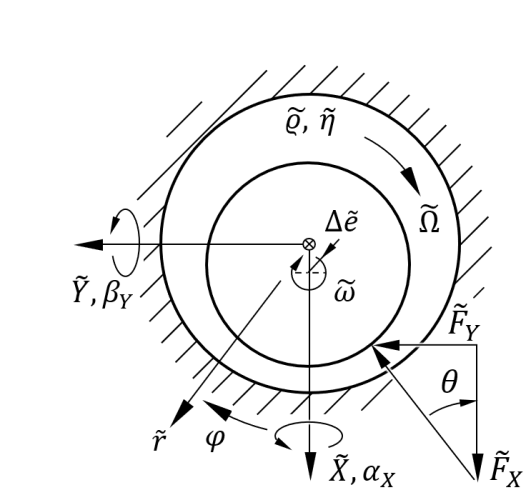
Clearance-Averaged Pressure Model
In the course of the project, the Clearance-Averaged Pressure Model, CAPM for short, developed at the Chair of Fluid Systems at the Technische Universität Darmstadt was extended and validated for the determination of rotordynamic coefficients. The model enables fast and reliable calculation of the stiffness, damping and inertia coefficients of media-lubricated journal bearings in pumps.
Results
Within the scope of the project, comprehensive physically based model developments have been carried out on the basis of complex CFD simulations, an integro-differential approach (Clearance-Averaged Pressure Model) and the Reynolds differential equation for determining rotordynamic coefficients. The calculation results were validated with extensive experimental investigations on two journal bearing test rigs. Overall, important influencing variables and their relevance for the various coefficients were identified through numerous parameter studies. In particular, the relevance of the virtual mass terms, the Lomakin effect and the relevance of the additional 36 coefficients compared to classical considerations were shown. The importance of the additional coefficients was evaluated on the basis of stability considerations and a practical application example from industry. Furthermore, an analytical calculation program (JoBs) for the determination of rotordynamic coefficients was developed, which is handed over to the companies and also enables them to carry out their own rotordynamic considerations. The findings can be directly taken into account in the design of media-lubricated journal bearings and enable a more precise and thus more cost-effective design of media-lubricated journal bearings in pumps.