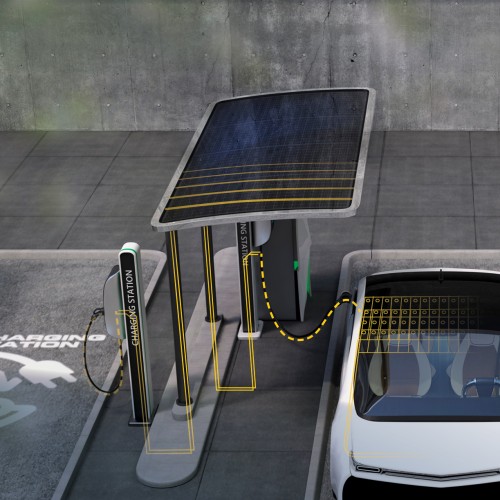
Tomorrow’s mobility
The demands on dynamically stressed components are increasing. Today, we are already researching ways to meet them.
In our research on design with fluids, the holistic view of systems and problems is seen as a central task of modern engineering. Consequently, our developments are driven by system understanding through physical modelling. In many areas of engineering practice, in addition to test bench and simulation capacities, the time factor in particular is in short supply, so that even today there is an enormous need to obtain design-relevant information from simple, analytical (and thus fast) tools. We examine the models and developed components experimentally on modern test benches and bring them to series production readiness with industrial partners.
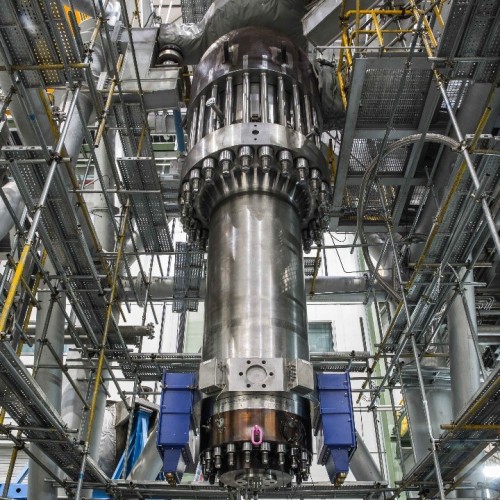
Availability of fluid power systems
Failure analyses show that the determining element for availability of fluid power systems is the lubricated narrow gap of plain bearings or annular seals. Due to friction and leakage, these machine elements also determine the efficiency of the system.
The Clearance Averaged Pressure Model (CAPM) is an efficient calculation method for incompressible fluid flow of narrow annular gaps. In addition to plain bearings and non-contact annular seals, the CAPM can also be used to reliably calculate and design modern machine elements such as fluid-lubricated plain bearings. The results of the CAPM are used to determine rotordynamic coefficients, unstable operating points, leakage and friction torques.
By using ansatz functions for velocity profiles and modelling wall shear stresses, the continuity equation and the full non-linear momentum equation can be efficiently solved. This allows the calculation of laminar and turbulent flow even without the constraint of other parameters such as eccentricity or axial flow/pressure difference. The prediction reliability is in the range of CFD simulations, but with a much lower computational effort.
For experimental investigation of gap flows as well as for verification and validation of the physically based models, various test rigs are available at the institute. Using extensive measurement technology (e.g. Hall and eddy current sensors), the relevant measured variables are recorded and archived in a comprehensible manner with the aid of a digital logbook being created at the FST. All measurement results are evaluated according to the current state of the art and subjected to extensive analyses regarding the measurement uncertainties.
Rotordynamic and gap flow test rigs
For the static and dynamic identification of gap flows, twotest rigs using magnetic bearings are operated at the institute. These test rigs allow the investigation of laminar as well as turbulent flows in narrow annular gaps with respect to their static and dynamic properties and effects on the rotordynamic. For variable gap geometry and operating conditions, rotordynamic coefficients can be determined experimentally.
Slip length rheometer
The Darmstadt Sliding Length Rheometer allows the measurement of wall slip of hydrodynamic lubrication. With the aid of the integral measurement principle – the frictional torque of the plate-plate rheometer and the lubricant film height at constant angular velocity are recorded – wall slip can be investigated for typical material pairings in hydraulics and sealing technology.
The starting point of our component development are physical models. These are based on physical axioms and serve as a foundation for vibration analysis. The models are validated in later development steps and used to optimize the components.
In mobile systems, the reduction of installation space and weight of vibration components is desired. Materials such as foams or adsorbents are suitable for this purpose due to their physical properties. Therefore, models for the optimization of material properties, such as the pore sizes of foams, are being developed at our lab.
In our product design we try to start the test phase at an early stage. To ensure that the boundary conditions at the system boundaries are correct, we rely on hardware in the loop. After model development, a prototype is built, with which the functionality is validated and the first problem areas are identified. After the functionality is validated, benchmark estimations are performed based on the model. If the benefit is sufficient, the next step is to design and manufacture the product with optimized parameters.
In order to test prototypes in a realistic test environment at an early design stage, hardware-in-the-loop tests are carried out. Here, only the component is needed as a prototype and the overall system is simulated in real time.
Unknown model parameters can be determined with the help of experiments. For this purpose, a prototype is measured in a series of tests at different frequencies on our hydropulser.
The availability of turbomachinery such as centrifugal pumps is often limited by their vibrational dynamic behavior. As a result of dynamic excitation by operating forces or imbalance, there is a response of the overall system, which is decisively influenced by the induced forces in narrow annular gaps, as they exist in plain bearings or annular seals. In fluid-lubricated plain bearings of centrifugal pumps, these induced forces are significantly influenced not only by the hydrodynamic effect but also by axial flow. In addition, turbulent flow conditions can occur as a result of larger bearing clearances and significantly lower viscosities of the lubricants. This laminar or turbulent flow inside the gap defines both the load carrying capacity of the bearing and the dynamic behavior of occurring vibrations. If the design is based on insufficient knowledge of the respective effects, resonance can occur in the worst case and subsequently lead to a total failure of the machine and maintenance-related expensive downtimes of the entire industrial plant.
The aim of the project is to develop a comprehensive database of rotordynamic coefficients and to identify unstable operating conditions, as well as to experimentally validate improved numerical calculation models for dynamic operating conditions based on the Clearance Averaged Pressure Model (CAPM) for fluid-lubricated plain bearings in pumps.
For sustainable energy generation, subsystems of modern power plants have to be highly flexible. Pumps are crucial components of almost all subsystems and thus have to be able to operate safely and efficiently in transient processes. The goal of the project is to understand the conditions of transient processes in flexible powerplants and derive requirements for the corresponding machines and components.
All those machines directly depend on the flow in journal bearings or annular seals, as their effects on the rotor dynamics limit the load and stability of the machine. The subproject “Rotor dynamic coefficients in unsteady pump operation” is handled by the Institute of Fluid Systems Engineering.
The aim of our subproject within the collaborative project is to develop an improved calculation method for annular damper seals and to expand the experimental database of rotordynamic coefficients developed in a previous project with respect to the special conditions of axial thrust relief devices in pumps.
Topic | |
---|---|
Development of fundamentals for transient operated hydraulic pump systems in flexible power plants: Flex Power Pant Pumps |
Report |
Media lubricated journal bearings in pumps |
Dissertation Summary |
Influence of molecular structure and additives on the slip length in hydrodynamic lubrication | Dissertation |
Flow behaviour in a small sealing gap | |
Vibrations in globe valves | Dissertation |
Energy generation from oscillating systems | Download (opens in new tab) |
Development of optimal control strategies for air-spring dampers | Download (opens in new tab) |
Numerical calculation of the internal sound pressure level of internal flows based on CFD simulations |
Download (opens in new tab)
Download (opens in new tab) |
Efficient numerical simulation of turbulence-induced flow sound with OpenFOAM | |
CRC805 – Active Air Spring, C4 | Book |
CRC805 – Mastering uncertainty in hydraulic systems, C9 | Book |
CRC805 – Fluid Dynamic Vibration Absorber, T5 | Book |
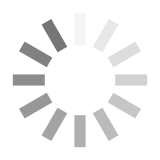
Error on loading data
An error has occured when loading publications data from TUbiblio. Please try again later.
-
{{ year }}
-
; {{ creator.name.family }}, {{ creator.name.given }}{{ publication.title }}.
; {{ editor.name.family }}, {{ editor.name.given }} (eds.); ; {{ creator }} (Corporate Creator) ({{ publication.date.toString().substring(0,4) }}):
In: {{ publication.series }}, {{ publication.volume }}, In: {{ publication.book_title }}, In: {{ publication.publication }}, {{ publication.journal_volume}} ({{ publication.number }}), ppp. {{ publication.pagerange }}, {{ publication.place_of_pub }}, {{ publication.publisher }}, {{ publication.institution }}, {{ publication.event_title }}, {{ publication.event_location }}, {{ publication.event_dates }}, ISSN {{ publication.issn }}, e-ISSN {{ publication.eissn }}, ISBN {{ publication.isbn }}, DOI: {{ publication.doi.toString().replace('http://','').replace('https://','').replace('dx.doi.org/','').replace('doi.org/','').replace('doi.org','').replace("DOI: ", "").replace("doi:", "") }}, Official URL, {{ labels[publication.type]?labels[publication.type]:publication.type }}, {{ labels[publication.pub_sequence] }}, {{ labels[publication.doc_status] }} - […]
-
Number of items in this list: >{{ publicationsList.length }}
Only the {{publicationsList.length}} latest publications are displayed here.